Neutronics for system codes
The 25th European Fusion Programme Workshop
Dubrovnik, Croatia, 27-29 November 2017
Neutronics for system codes.
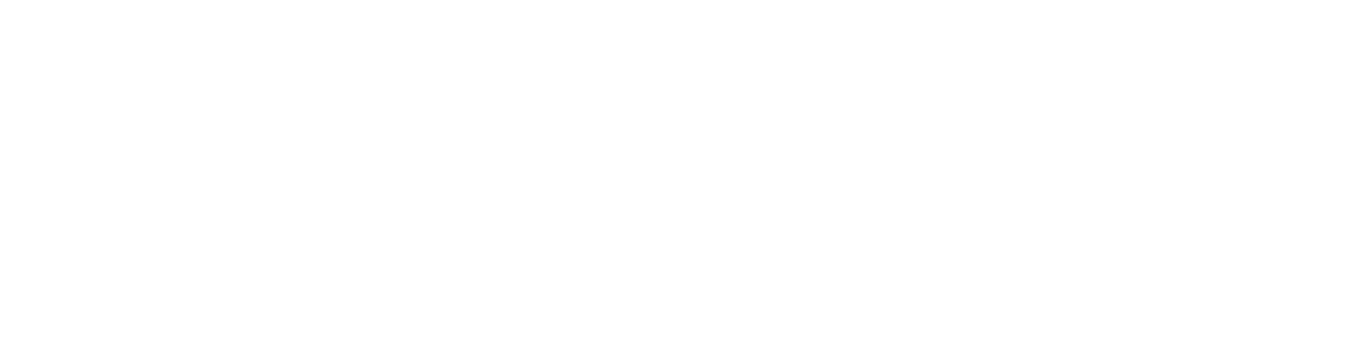
by Jonathan Shimwell

To perform automated parametric multiphysics analysis of breeder blanket designs with an aim of optimising the design.
Objective
To perform automated parametric multiphysics analysis of breeder blanket designs with an aim of optimising the design.
Neutronics for system codes.
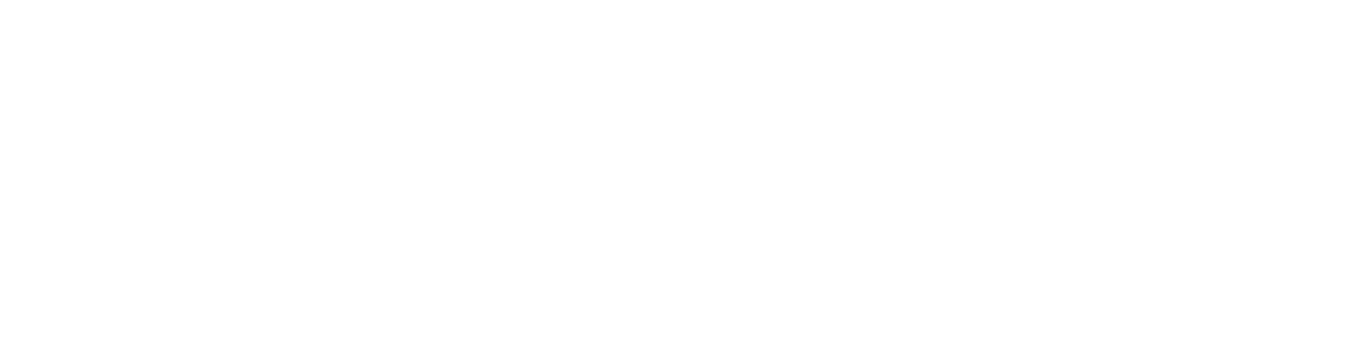
by Jonathan Shimwell

Selection of design parameters
Parametric CAD construction
Neutronics simulation for TBR and EM
Conversion to unstructured mesh
Neutronics simulation for volumetric heating
Conversion to engineering mesh
Simulations to find stress and temperature
Evaluate design
Conversion to neutronics model
Interpolate performance & design sensitivity
Model generation

PythonOCC
Salome
Parametric
HCPB model
FreeCAD
Parametric
HCLL model
Neutronics model
MCNP
constructive
solid geometry
MCNP
unstructured
mesh geometry
Serpent
STL geometry
Serpent
unstructured
mesh geometry
Engineering
model
Parafem
model
Code Astra
model
Trelis
Hex mesh
Abaqus
Trelis
Hex mesh
OpenFoam
STEP to STL conversion
Geometry conversion
MCam / McCad
CAD to CSG
converters
Meshing
Trelis
Tet mesh
Ensight Gold
GMesh
Salome
MED
Avoid the use of constructive
solid geometry (CSG)
CAD model
Convert to CSG model
Assign materials
Parameterise CSG model
Neutronics simulation
CAD model
Convert to STL model
Assign materials
Parameterise CAD model
Neutronics simulation
No spline support. Void Generation
Lack of tools
Cell based
Rapid and controllable
Mature software
File based
Optimal parameters
Optimal parameters
CAD
model
Traditional CSG work flow
Alternative STL work flow

Blanket geometry construction
Blanket envelop input
Feature recognition
Output geometry

Front face
Edge to fillet
Top face
Variable detail blanket geometry


Surface deviation = 0.01mm
Surface deviation = 1mm


Homogenised first wall
Detailed first wall


Blanket geometry construction
Customizable cooling pipe layouts for the internal cooling plates

Blanket geometry construction

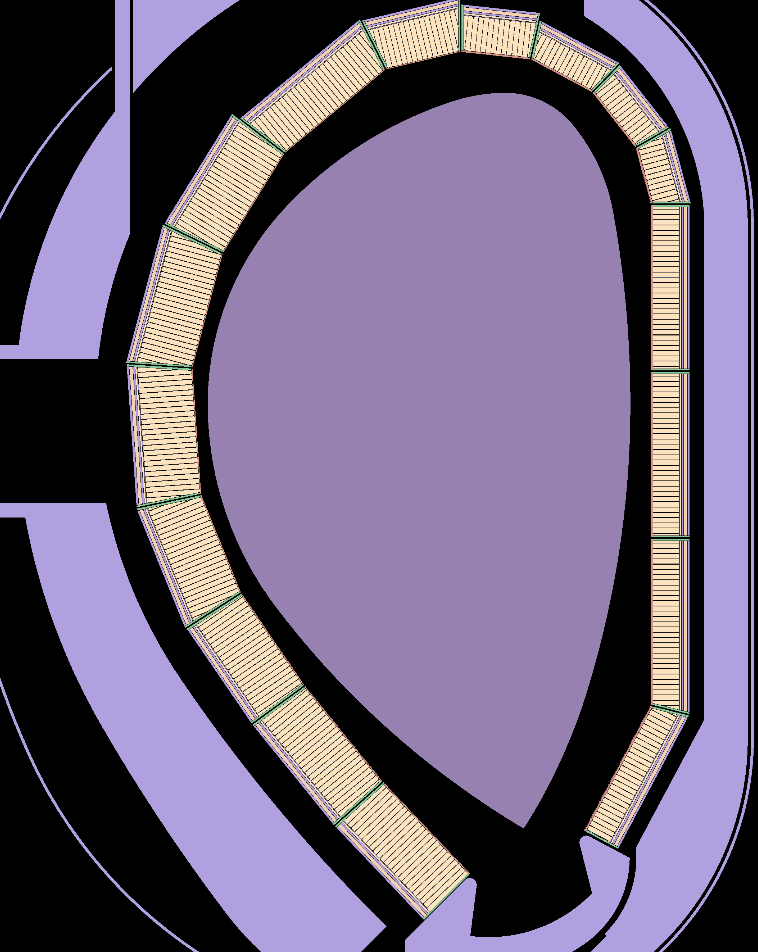

Blanket envelopes from the entire reactor can be parameterised
HCLL blanket geometry parameter options

-
Armour thickness
- First wall thickness
- First wall cooling channels (height, width, pitch)
- End caps thickness
- Lithium lead poloidal distance
- Cooling plates poloidal distance
- Cooling plate coolant channels (height width)
- Toroidal distance of rear components (plate, lithium lead, coolant, divider and cap)

HCPB blanket geometry parameter options
- Lithium ceramic poloidal distance
- Neutron multiplier poloidal distance
- Choice of breeder material Li4SiO4, Li2SiO3, Li2ZrO3, Li2TiO3
- Choice of neutron multiplier Be, Be12Ti, Ba5Pb3, Nd5Pb4, Zr5Pb3, Zr5Pb4


Computing techniques
Cloud computing and containerization of code was used for this project.
Containerization allows for codes to be combined with their dependencies packaged into a container and deployed on compatible infrastructure.





Serpent II
Nuclear data





Docker








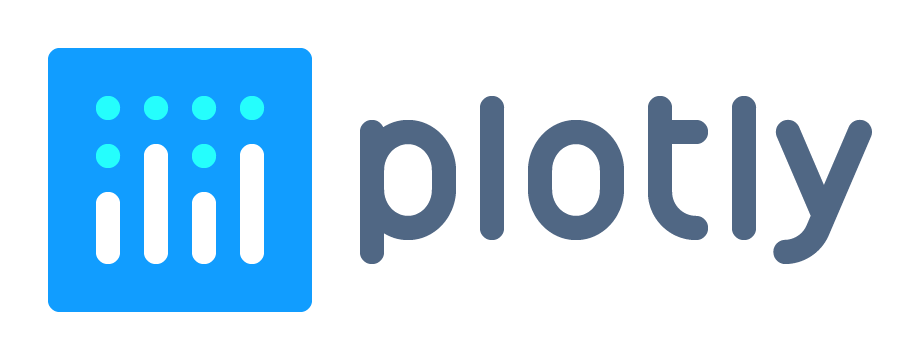
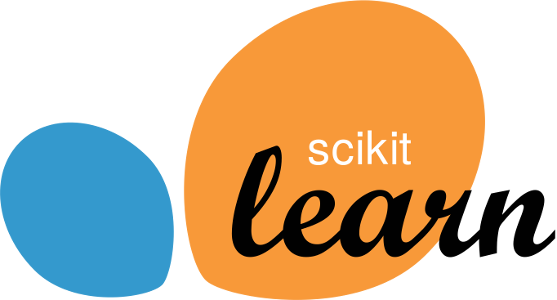
Computing techniques

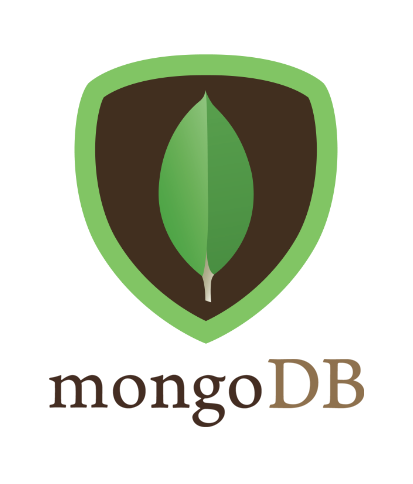
Docker






Singularity
Swarm
Orchestration
Compute
Containerize
Storage

Day of the week
Cluster utilisation
100%
Your local computing cluster?
Mon
Tue
Wed
Thu
Fri
Sat
Sun
Example parameter study



Interpolation of results
Li4SiO4 with 60% 6Li and Be

Tritium production
Li4SiO4 at 60% 6Li enrichment with Be
Fitting the data using Gaussian Processes and training datasets
The Gaussian functions found fits the provided data points very well?
Fitting the data using Gaussian Processes and training datasets
Red points are used for fitting
Blue points are used for testing the fit
Volumetric heating simulations
Due to the use of CAD throughout the project the same model can be used to obtain TBR, volumetric heating, temperature and stress.
Procedure for obtaining volumetric heating
- Neutron and photon heating simulated and results passed to engineering codes
- Parametric CAD models created using Python scripts and automatically converted to neutronics models
- Unstructured mesh applied to the geometry





Automated hex and conformal tet meshing


Neutronics mesh?
Engineering mesh
Do we need meshing algorithms designed for neutronics tallies?
Mesh element density should be concentrated in areas of high gradient.
Simulation time increases with number of mesh elements.
Meshing
Fully automated hex meshing of the geometry. Exporting to Abaques format for use with MCNP 6 unstructured mesh and Open Foam format for use in Serpent II.

Volumetric heating
Heating values obtained on unstructured mesh that conforms to material boundaries.

y

Volumetric heating


Li4SiO4
Be12Ti

Component | Be12Ti | Be |
---|---|---|
Lithium ceramic | 15.9 | 17.2 |
Eurofer first wall | 6.2 | 5.8 |
Tungsten armour | 28.1 | 26.4 |
Neutron multiplier | 4.8 | 5.0 |
Heating W/cm3
with 60% 6Li enrichment
Automatically identifying regions




First wall heat flux
Coolant outlet
Coolant inlet
Current work
- Thermal mechanics analysis of the breeder blanket
- Reviewing codes and standards for suitable design rules to apply to the analysis


- Collating temperature dependent material properties for use in engineering analysis.



Automated Portable
Parametric
Scalable
Neutronics
Conclusion
Figure shows tritium production within EU DEMO
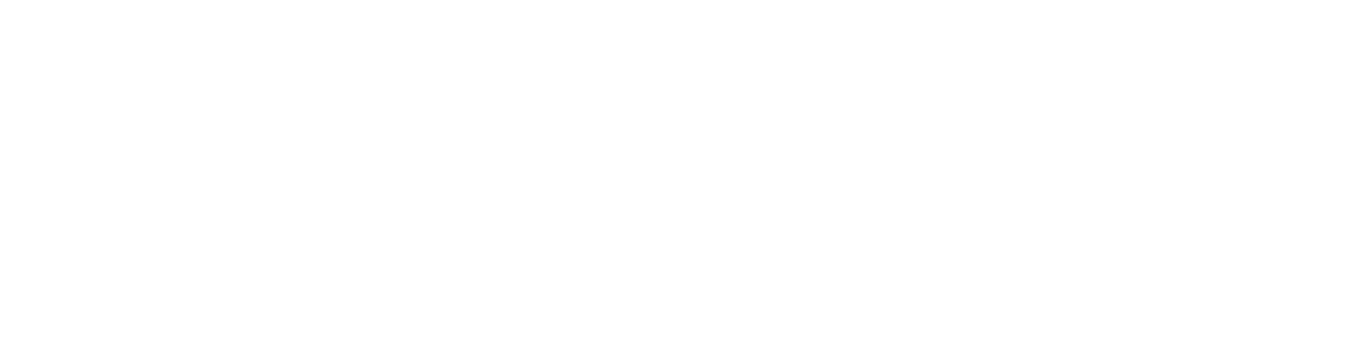
Project carried out as part of a WPBB Eurofusion Engineering Grant
Neutronics for system codes
By Jonathan Shimwell
Neutronics for system codes
Dubrivnik presentation
- 661